Renowned for its many qualities, such as warmth and comfort, sheep’s wool is a natural fibre widely used in the textile industry. Before learning more about this sustainable material, we offer you a brief history. Sheep, like other animals, are unable to moult. Shearing is therefore necessary for its health.
Wool, origins and history
Since prehistoric times, nearly 10,000 years ago and even before domestication, sheep have been used for their meat but also and above all for their wool.
Around 2500 BC, weaving looms, although rudimentary, began to emerge throughout the Mediterranean region and allowed wool to be worked much more efficiently. This was further strengthened by the invention of the fuller’s wheel around 1200 BC, which made it possible to degrease and soften sheep’s wool.
Later, in the 13th century, the wool trade intensified and became one of the main sources of income for countries like the Netherlands and Italy.

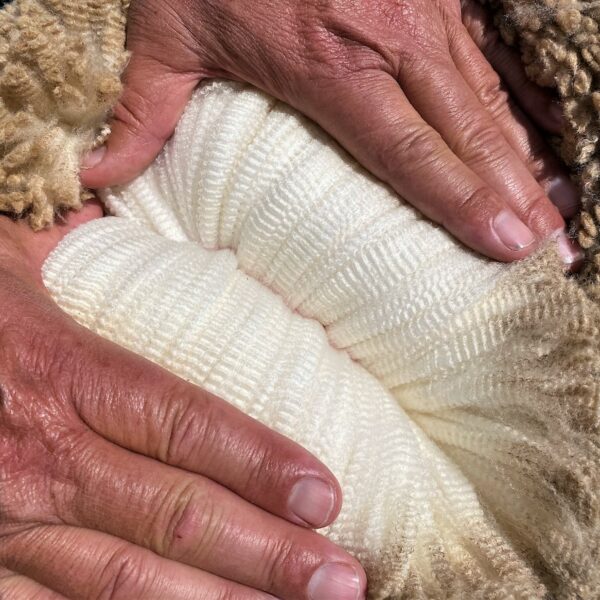
The characteristics of wool
But what is wool after all? It is a natural material made up of keratinous fibres from the fleece of the sheep. Sheep’s wool is therefore a durable and 100% biodegradable material.
Sheep’s wool against the elements
It is also a versatile material that was used very early in the history of mankind and for good reason: in addition to being elastic and light, practical for moving around, it is very resistant to the elements. The fibre can absorb up to 30% of its weight in water without getting wet, no less! In addition, it has exceptional thermal and insulating properties.
The different types of sheep’s wool
There are different types of raw sheep’s wool. In France alone, there are over 50 different breeds of sheep! Moreover, not only the quality of the wool, but also its appearance, can change depending on the type of sheep (and yes!) and its environment. One of the best known is Merino wool.
Now let’s get down to the nitty-gritty: how is sheep’s wool harvested and processed? What is behind our favourite jumpers?
The wool’s journey: from shearing to shops
Every year, sheep produce a new fleece ready to be classified, scoured and processed. Let’s get to know the secrets of the wool’s journey, step by step: from shearing to finished products.
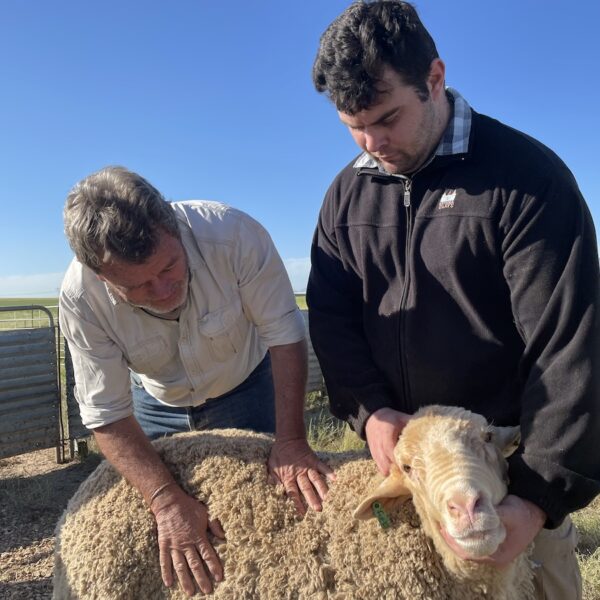
1. Shearing
The raw wool is first collected by a shearer, who will proceed with the shearing. This is done either with tools such as “forces” or with a mechanical shearing machine called “hand shears”. The natural wool thus obtained is a one-piece fleece. The fleece is then thrown onto a sorting table and sorted according to the quality and characteristics of the fibres.

2. Classification of the wool
After shearing, the wool is classified in two different ways according to its characteristics and appearance:
- Long uniform wool fibres for worsted spinning,
- The shorter fibres for carded spinning or other applications.
Then it is time to prepare the wool for spinning. This is a complex process that requires real expertise.
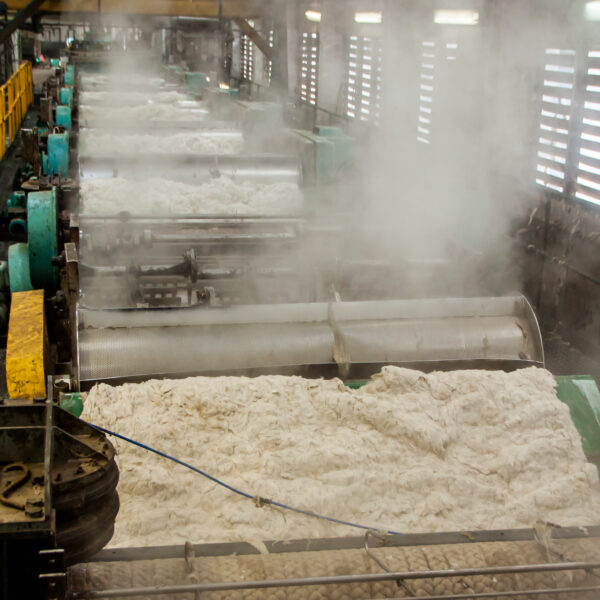
3. Preparing the wool
The processing of the wool fibres starts with washing in hot water and then with detergent. The aim? To remove dust and grease in the first instance.
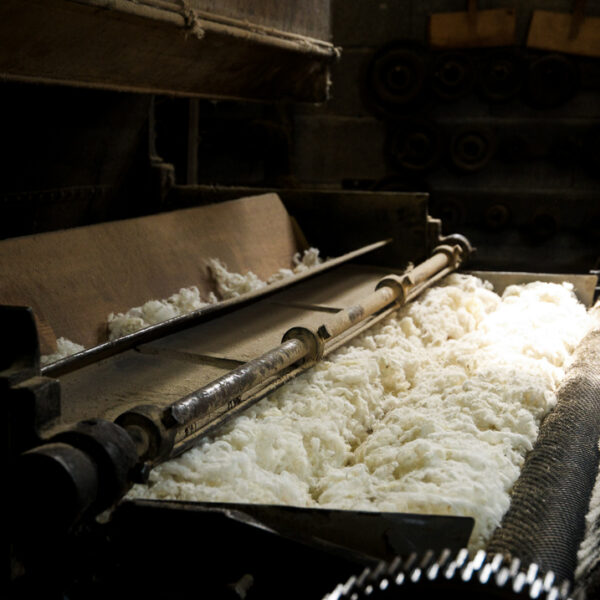
4. Carding
Once the wool has been washed, it undergoes a process called “carding”. This stage opens up the wool fibre and prepares it for the next stages of processing. At the end, the wool obtained is in the form of :
- Roving for carded spinning
- Ribbon for combing.
The wool is then passed through metal teeth to align the fibres and prepare them for combing.
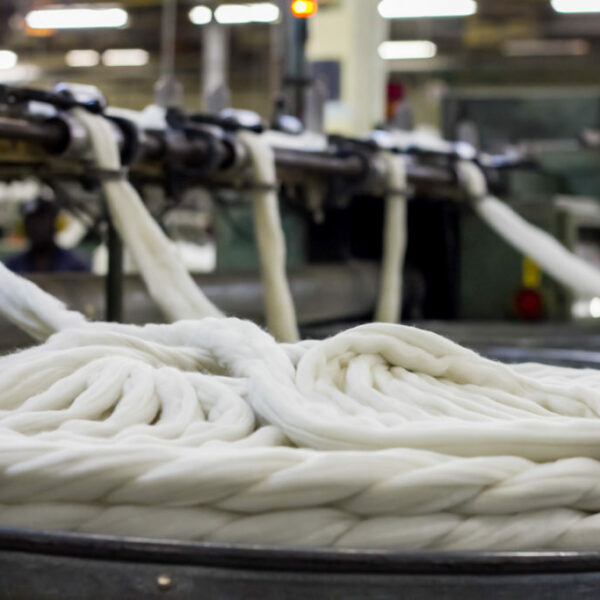
5. Combing
The sliver from the carding machines is drawn out before combing to align the fibres, this is the preparation. This is the preparation stage, followed by the actual combing stage. The combing process is a crucial step in ensuring the quality and purity of the wool being processed.
The longest strands are formed into a thicker sliver. This formed sliver is then stretched and reduced in thickness. The final processing step is to obtain a stronger yarn for knitting or weaving from the combed, tapered rovings.
A little tip for recognising the different yarns:
- Combed yarns are fine and smooth.
- Spun wool yarns are more textured and voluminous.
Once the yarns have been formed, it is time to process them into finished products.
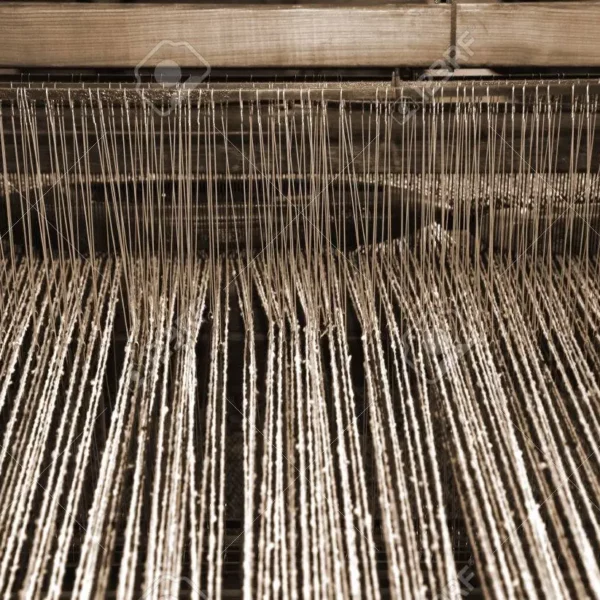
6. Processing
Wool yarn can be processed in several ways: knitting, for example, or weaving. The dyeing of wool can be done at almost any stage of the production process, either during the formation of the ribbon, directly on the yarn or on the finished product!
Now that you know all about the many properties and processing of sheep’s wool, you will never look at your jumpers in the same way again!